So you want to buy a Storage or Garden Shed in the Seattle-Tacoma area?
This guide will help you decide what to look for and what to stay away from.
When many people think of the Puget Sound they associate the region with rain, humidity and moisture. We have been nicknamed the “Pacific North WET”, amongst others, and it is indeed a fact, especially for Washington State.
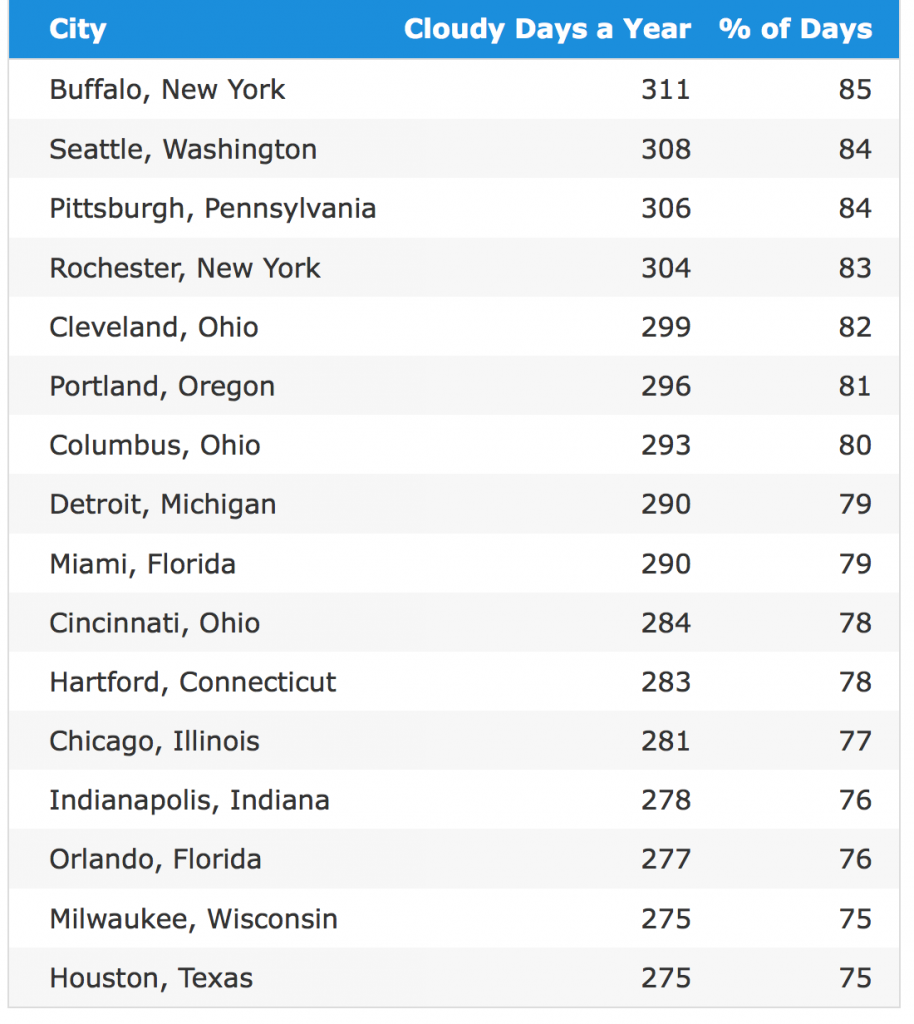
Equally unfortunate is the regions rainfall.
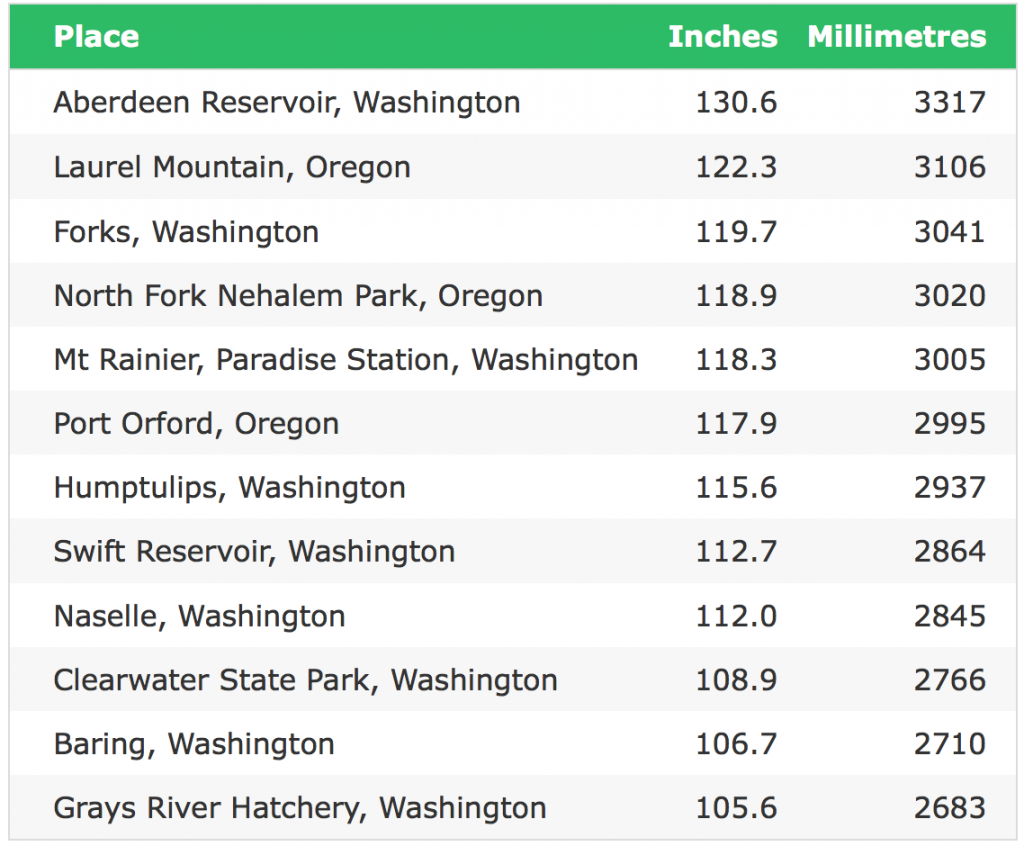
Knowing that we experience this type of weather regularly is actually a good thing when it comes to construction standards as we know for sure what to expect and can build accordingly. Unfortunately there are many National Shed Companies, un-licensed and un-trained “builders” and even some licensed contractors that sell sheds but choose to simply ignore best practice in order to make a quick sell and fill their pockets with ill-gotten profit at the buyers expense.
Before I address the Building issues in depth I would like to take a quick look at Property Crimes in the Seattle-Tacoma area. Property crimes include theft, break-ins, burglary and vandalism. Security is a big deal these days and the items you choose to put into storage probably have a personal value to you, we we work hard to save for our goodies these days and that is why we choose to put it into storage rather than purchase new more frequently then necessary. Our property also has a street value and is a very lucrative for thieves, the easier you make it for them the more likely you are to become a victim.
Here’s how the Seattle – Tacoma area measures up to similar metro areas for property crimes.
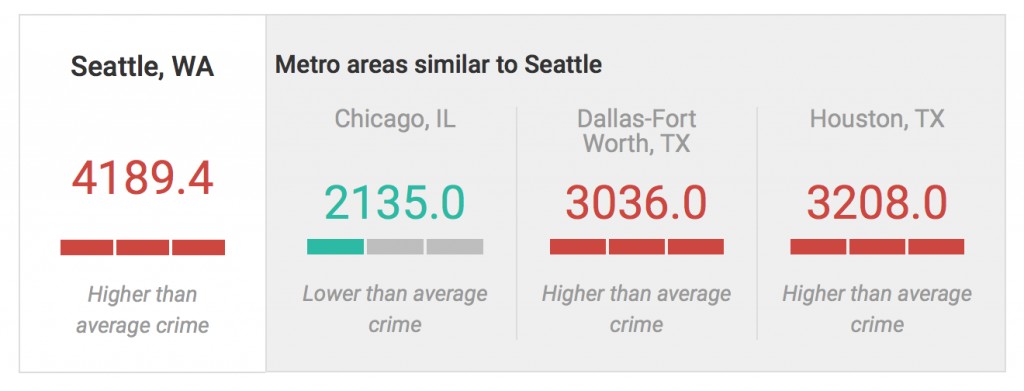
Addressing these two aspects of life here in the PNW in relation to “Shed Health” and Security is just a start of many aspects, there are some very basic building practices that you can look for to keep yourself from inadvertently squandering your hard earned savings. Purchasing a Shed, Barn or the Accessory Building should be an investment rather than a liability.
In all cases the type of Building Materials, or lack thereof, will dramatically impact whether or not your purchase is an actual investment.
Let’s start with the building materials typically used to build sheds you will encounter from typical shed vendors.
OSB vs Plywood:
While OSB (Oriented Strand Board) is generally cheaper than plywood, it is heavier and not as stiff as plywood and can result in soft squeaky floors under weight. The biggest complaint against OSB is that it doesn’t handle moisture very well so it is more suited for indoor use. Moisture also affects the strength of plywood; so while exterior glued plywood can be used outdoors, it works best when moisture content remains low.
OSB left, Plywood right
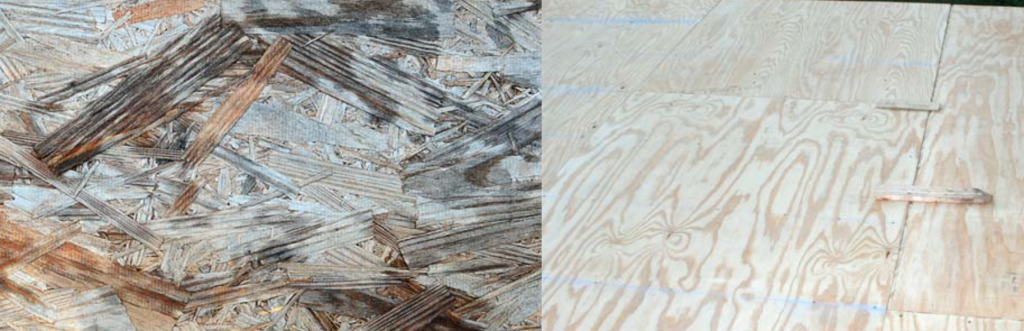
OSB is quickly becoming popular amongst builders as it is less a expensive product compared to its Plywood counterpart, up to 25% cheaper depending on the size used. For the most part OSB shares many of the same strengths as plywood such as shear strength, and if handled and installed properly OSB is fine for some applications in shed construction. The problem is OSB is rarely installed per manufacturer suggestion.
Irreversible edge swelling has been the biggest knock on osb. Manufacturers have done a good job of addressing this issue at the manufacturing facility and during transportation by coating panel edges. But the reality is that builders don’t limit osb use to full-sized sheets. The edges of cut sheets are seldom if ever treated in the field. Houses under construction get rained on. And if you use osb in an area of very high humidity, like over an improperly vented attic or over a poorly constructed crawlspace, you are asking for trouble.
Once water gets into osb it is very slow to leave. The longer that water remains within osb the more likely it is to rot. Wood species has a significant impact. If osb is made from aspen or poplar, it gets a big fat zero with regard to natural decay resistance. When osb is exposed to wet conditions, it expands faster around the perimeter of the panel than it does in the middle. Swollen edges of osb panels can telegraph through thin coverings like asphalt roof shingles.
When OSB is used for flooring in rainy climates it will almost certainly have an accelerated decay as we track the moisture in every single time we walk into the shed. Painting OSB will help seal OSB (and Plywood) but will require regular maintenance that is often neglected or is an oversight due to the fact that most of the floor is hidden once the building is filled with your belongings.
As for use in Siding OSB is just fine as these OSB siding products are treated on both sides against rot and mildew (and certain insects), pre-primed on the exterior… however buyers should beware if you see OSB being used for roof or floor sheathing.
Shed Security:
If a thief wants in, they will get in. Thieves are brazen these days and occasionally there are reports of shed burglaries by removing whole siding sheets and even using cordless tools to cut man sized holes in the back of the buildings to gain entrance. Most times entrance is gained through doors and large windows though.
Most thieves will attempt the easiest targets, when they see a fortified entrance they will likely move on to an easier target that doesn’t require them to make unnecessary noise to gain access.
Many of sheds sold use some type of locking door handle, the most popular is the T-Handle door lock.
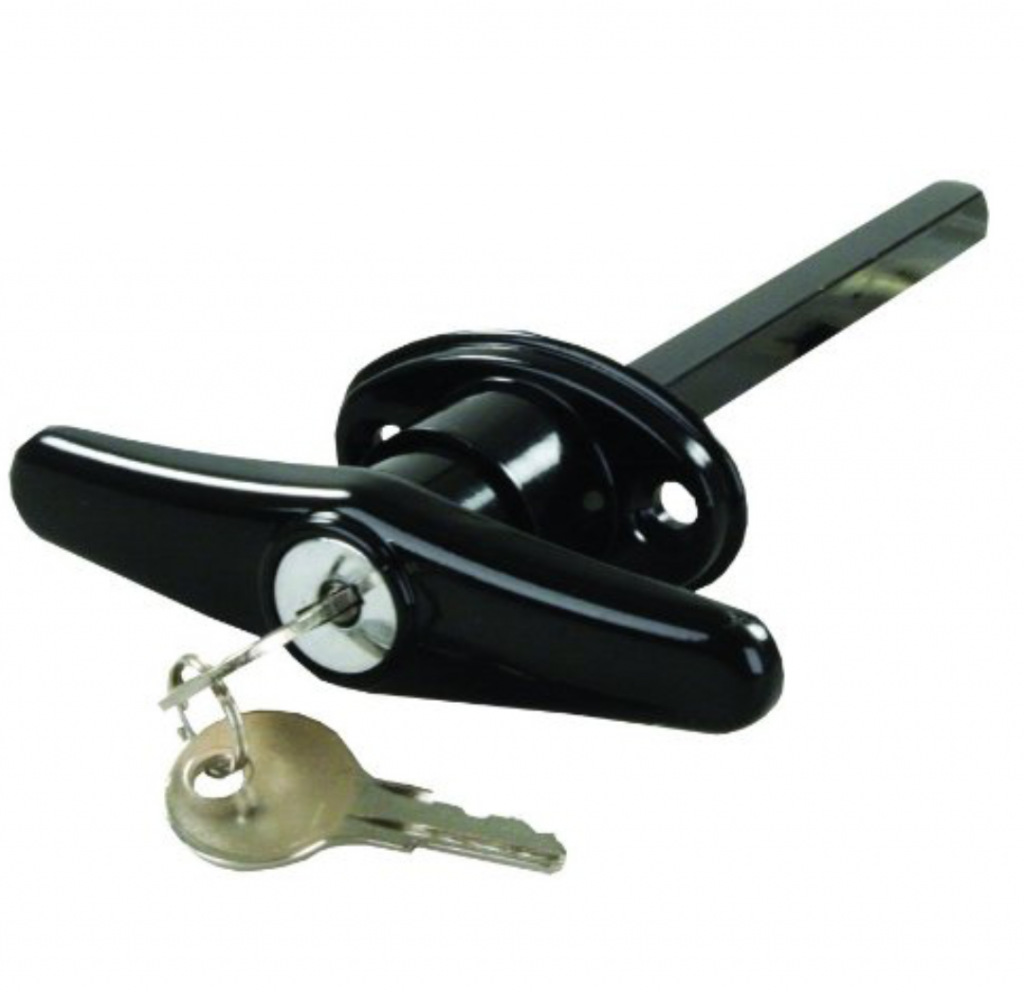
There are a couple of issues with these types of locks that should be considered. These locks are cheaply made and widely available, due to their popularity they are mass produced and there is an ever growing need for Master Key availability to gain access to change the lock when customers lose keys or for Rent to Own companies to use when performing an involuntary repo. Thieves know this and have ready access to master keys which are widely available from sources that can be found on the internet including shed suppliers and even Amazon, they can simply order the master key.
These locks and keys are numbered, if you have a key with a number 400 or 500 you already have a master key!
Even without the extremely easy to get master key these locks can be hit hard with a hammer or other blunt object and will spin freely, the noise from the hit is about the same as a car door shutting and a thieve will prefer this type of entrance over using power tools, force or violence to gain entry.
Worse yet, there are only 2 screws on the outside and one hex bolt holding the lock on the door to begin with, T Handle door locks are an easy target. If you plan to purchase a shed with a T-Handle you should ask for a secondary locking mechanism or add a bolt style yourself.
Piano Hinges and non framed doors:
Ever wonder why the sheds at the local big box stores have no doors, or damaged doors hanging or completely missing? It is likely because vandals have easily gained access through these poorly built doors that typically use cheap piano hinges and lack a door frame at all, or maybe the cheaply built door simply failed on its own?
Many of the mass produced sheds you will see use the exterior trim of the door as the frame, this trim is typically an OSB or Engineered lumber product and the hinges utilize several ⅜ inch screws between two pieces of the doors trim. These doors are easily defeated and after time can fall apart just by normal use or if the door is accidentally left opened to swing freely in the wind.
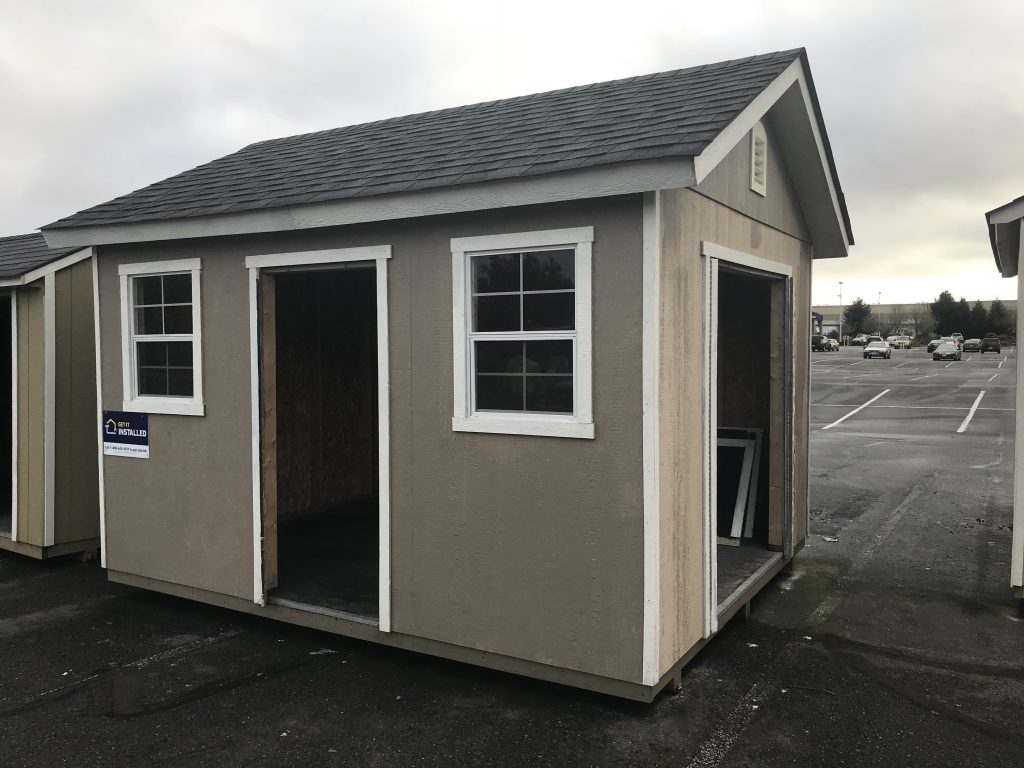
What should you look for?
There are a lot of anti-theft products being sold for security of shed doors, but starting with a framed door is paramount for door life and shed security, there are many variations of door frames available and you should look for the frame to be made out of at least 2×3 or 2×4, a full frame, not just a door stiffener or simply one “stick” holding it together.

In addition to framed doors you should inspect the type of hinges and the hardware used to mount them, a good hinge with carriage bolts and locking nuts are extremely difficult to defeat and would be thieves will likely move to an easier target immediately.
A good bolt style latch that uses carriage bolts is also a great deterrent against theft or vandalism, most shed contractors will be able to install carriage bolts and stout piano hinges for a nominal charge, unfortunately most shed companies will not entertain the option.
Carriage bolts can also be installed on external hinges, such as external T-Hinges or external steel piano hinges.
Carriage bolts have rounded heads on the outside that cannot easily be removed with a wrench, pliers or similar tool, they would need to be cut off or pulled completely through the door frame (if there is a frame) and when paired with a nylon lock nut on the inside a thief would need to make a huge amount of noise to gain entry.
Bolt latch with carriage bolts
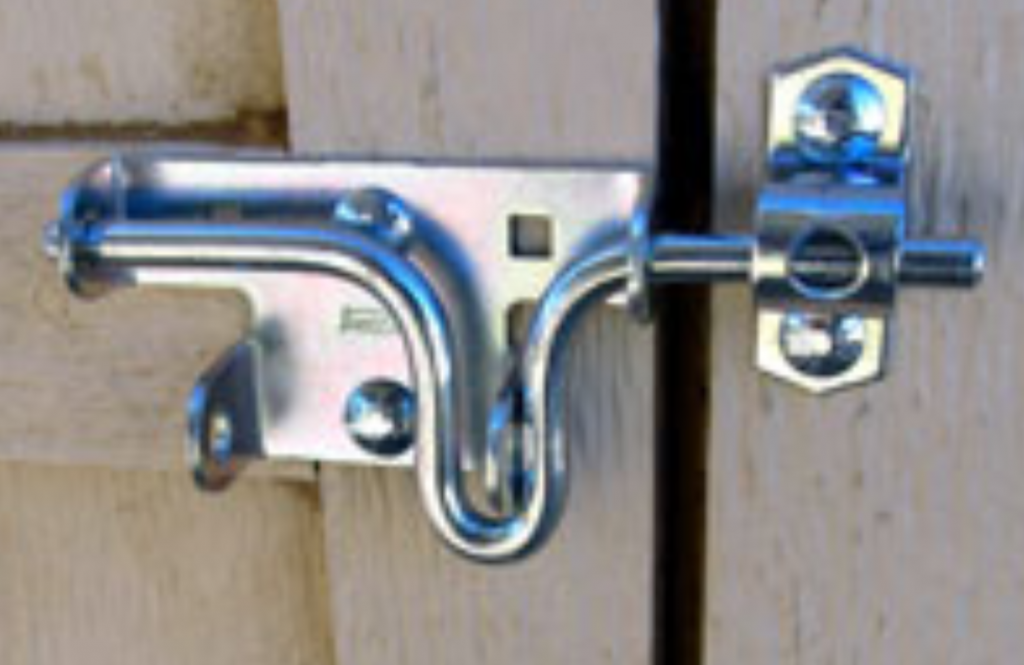
Hopefully this short article has made you a more informed buyer and will help you understand what to look for when shopping for your next (or first) shed. A good shed builder should be able to accommodate these simple requests to use different construction materials and/or security upgrades.
Also, and this is very important, always be sure to get confirmation that whoever installs your shed, or builds it for you is a Licensed Contractor, licensed contractors have the necessary bond and insurance to protect you, your project and your property, just because the big box store sent them out does not mean they are licensed and you are protected, the actual person building your shed must be licensed for you to be protected.
You can easily verify a contractors license using this link: https://secure.lni.wa.gov/verify/
PNW Shed Buyers Guide -Part 2 coming soon ….